Fast and efficient repalletizing from pallet to pallet
Flexible, time- and cost-saving automation solution for your warehouse
When depalletizing and repalletizing products of various types, sizes and packaging, many companies still rely on manual labor. In addition to constantly rising wage costs, high physical stress leads to unpredictable staff absences and frequent employee turnover.
The new repalletizing system from PREMIUM ROBOTICS automates, accelerates and optimizes a wide range of logistics and palletizing tasks. It relieves employees and stands for secure and reliable processes that save time and costs. The unique gripping, conveying and handling system enables robots to handle an almost unlimited range of cartons, packaged goods and packs quickly, reliably and efficiently. With its innovative roll-on gripper system, the repalletizing system can easily lift, transport, align and stack even hard-to-grip packaged items.
Repacking directly from pallet to pallet or onto a conveyor is generally possible without layer depalletizers, shuttle intermediate storage or complex conveyor technology.
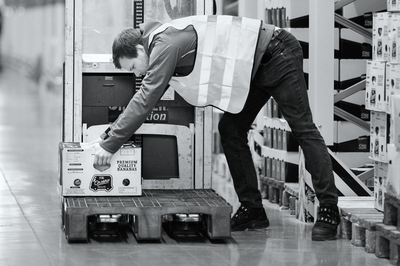
Physically hard work:
Your advantages at a glance
High performance
Repacking capacity:
to 300 packs per hour per robot
(depending on container type)
Depalletizing capacity:
up to 400 packs per hour per robot
(depending on container type)
Higher power possible with multiple handle
(Stack).
SUITABLE FOR ALL
Compatible for all common pallet formats: Euro, half, industrial, container, American and Asian pallets up to 2.4 m high. Even if they are not perfectly stacked.
LOW COSTS
Depending on the scope of tasks, the basic version involves manageable investment costs that pay for themselves in a very short time. Inexpensive expansion options are available for task-specific additional applications. By means of service package incl. Remote maintenance and predictive maintenance can minimize downtime and increase availability.
ALMOST UNLIMITED PRODUCT RANGE
Handling of almost all containers with dimensions from 15 × 15 cm to 68 × 68 cm and weight up to 20 kg.
Handling of intermediate layers. Short cycle time and gentle handling.
High flexibility with regard to staging situation and target position.
LOW SPACE REQUIREMENT
Plants and systems from PREMIUM ROBOTICS take up very little space. They can be integrated into almost any logistics environment and are expandable as needs change.
Minimum size: 3.5 × 5.5 m
When using several robots, the space required per robot can be significantly reduced.
SIMPLE OPERATION
By means of clearly structured, easy-to-use operating software, products and tasks can be intuitively taught in a very short time, packing patterns generated and complete jobs created.
Plants and systems from PREMIUM ROBOTICS are available either as a stand-alone solution or as an integrated variant with connection to the warehouse management system.
A system. Countless possibilities.
Flexible repackaging with intelligent gripping and handling technology: Whether large, small, closed, perforated or open-topped cartons with different contents. Whether trays with beverage cans, glasses, plastic cups, or film-sealed packs: with the repalletizing system in combination with supporting sensor and image processing systems, robots are able to transfer not only ideal-typical but also less stable, unusual packs from the consumer goods industry directly from a storage pallet to the delivery pallet. Faster, more accurately, more persistently and more gently than even the most skilled warehouse worker could ever manage.
MANAGEABLE PRODUCT RANGE
Size: from 15 × 15 cm to 68 × 68 cm
Weight: up to 20 kg
Other sizes upon request
PALLET FORMATS
All popular formats
in wood and plastic,
Special sizes upon request
APPLICATION EXAMPLES
Varietal repalletizing
- to reduce the height of the pallet
- to other pallet sizes
- With intermediate layers
Repalletizing for mixing different grades in the same containers
- Mixture block by block
- Mixture column by column
- Mixture in layers
Repalletizing for mixing different containers
- Mixture block by block
- Mixture in layers
- Mixture in layers with intermediate layers
Solutions from a single source: Turnkey logistics facilities
The core competencies of PREMIUM ROBOTICS and thus the key to successful automation lie in the areas of gripping and handling technology, robotics and control technology, and AI-based image processing. With the know-how of our experts and many years of experience in subcomponents and complete systems, software and hardware, maintenance and service, consulting, training and support, we offer you the complete range of services from a single source.
Recirculation process
To pick up the packs, the roll-on gripper lifts them with a rubber roller on the front side and then moves them underneath.
Turning process
Packs can be turned on the gripper from lengthwise to crosswise or vice versa. Just as the filing situation requires.
Image processing
The localization of containers is made possible by a 3D camera and an AI-supported algorithm.
Interleaves
Layer pads can be removed from source pallets or placed on target pallets using suction technology.
The range of articles, quantities, cycle and operating times, structural boundary conditions as well as upstream and downstream processes have a significant influence on the selected solution. This should ultimately be the optimal answer to the requirement you set.
With our integrated approach as well as the much-cited looking beyond the end of one’s nose that is lived at PREMIUM ROBOTICS, we succeed in convincing customers both in the retail sector (e.g. in the food industry) as well as in the logistics, service, manufacturing and equipment sectors with high-quality, reliable and efficient system solutions.